As Florida grapples with the challenges posed by stronger hurricanes and other impacts from climate change, the construction industry is challenged to become more innovative by embracing new materials and technology to create stronger, more sustainable, and less expensive buildings.
Could LEGO-like buildings be the answer?
“This is something that’s so simple. I can’t believe that no one has thought of this before,” said RENCO USA President Kenneth Smuts.
Smuts started his career as a nuclear construction engineer, so he’s used to complexity. He went on to spend four decades in commercial construction and is now leading RENCO USA. The company’s mission is to revolutionize the construction industry by simplifying building while making it stronger and more sustainable.
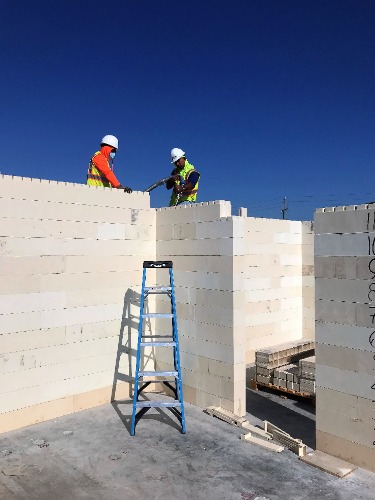
A Greener Way to Build
Think of it like a real-life LEGO kit—molded blocks that interlock and create entire structures. RENCO is short for “renewable composite” and is made of naturally occurring and repurposed materials. It weaves together repurposed glass fibers, resin, and stone into a powerful new material stronger than concrete and rated to withstand a Category 5 hurricane. Repurposed materials make up to 40% of the mix in RENCO products, meaning materials destined for the landfill are reused instead.
“There are so many industries that have scraps or overbuy materials that can be repurposed,” Smuts added. “For example, RENCO uses repurposed glass fibers and resin left over from the massive boat building industry, which helps to reduce waste.”
Reducing Energy Consumption
By simplifying construction into a LEGO-like kit, RENCO buildings can be assembled much faster, reducing time on the job and energy consumption. It only takes about two hours to train a person to build with RENCO, so construction projects aren’t delayed due to traditional labor shortages.
“We just cut the ribbon on the first RENCO USA housing complex in Palm Springs, Florida, and finished it in record time,” Smuts said. “With 11 unskilled workers, it took about eight weeks to assemble each of the four identical three-story buildings.”
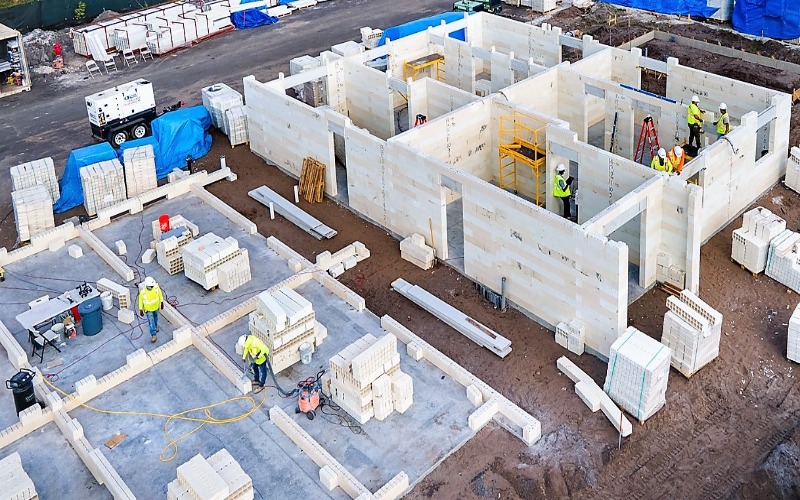
Decreasing Construction Waste
At a conventional construction site, you’ll see a flow of dumpsters hauling away heaps of cut materials, scraps, and overpour from concrete. At a RENCO site, there aren’t big dumpsters—there is no cutting to do since every building is like a kit.
“Even when RENCO parts are molded, any tailings to mold the product are added back into the mix,” Smuts explained.
Also with conventional construction, crews buy an average of 10% extra materials to cut and fit materials and fix errors on site. With RENCO, crews have about 2% extra materials, which is saved for future projects if they’re not needed.
Less Energy to Transport & Build
RENCO also requires less energy to build and transport because the material is much lighter. RENCO blocks weigh about 20 percent of the weight of concrete blocks.
“For every one truckload of RENCO’s composite materials, it takes four trucks to deliver the same number of heavy concrete blocks,” Smuts added. “That’s a big difference.”
In addition, crews don’t need heavy equipment or power tools—no exterior scaffolding, big cranes, cutting, burning, welding, or grinding. To build with RENCO, all that is required is a fork truck to lift the materials, a glue gun powered by a small generator, and a mallet.
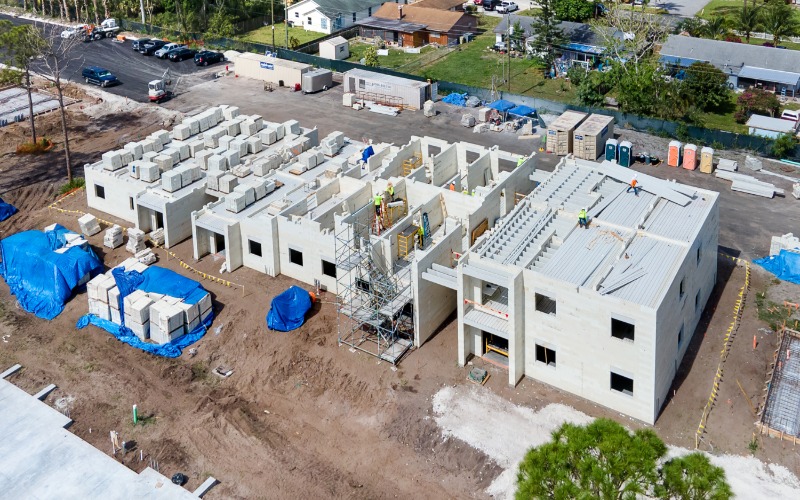
A More Sustainable Building
“The greenest building is the building that doesn’t need to be replaced,” Smuts stressed. RENCO buildings are rated to last two to three times longer than conventional construction, which reduces the need to rebuild every 25 to 40 years.
As the impacts of climate change worsen, RENCO construction is easier to insure because it has a longer lifespan than typical construction. It’s also rated hurricane and earthquake-resistant and resistant to fire, water, mold, termites, and pests. It simply won’t rust or rot, and nothing will consume it.
Reducing Construction’s Carbon Footprint
The reality is greenhouse gas (GHG) emissions from the building and construction sectors account for approximately 40% of global GHG emissions. The Athena Sustainable Materials Institute, a non-profit that researches the carbon footprint of construction, examined RENCO’s material. Its findings were staggering.
Researchers found that RENCO has a carbon footprint that contains 82% less embodied carbon than structural steel and 62% less embodied carbon than reinforced concrete.
Central to that smaller environmental impact is the fact that RENCO reduces the use of concrete. Cement, the core component of concrete, is responsible for 8% of planet-warming carbon emissions—more carbon emissions than the entire airline industry.
While nearly all modern structures have a concrete foundation, RENCO uses zero concrete above the foundation, which is a breakthrough in green construction and the effort to reduce the use of climate-warming cement.