The promises of a lighter, cheaper battery that would give longer range has been elusive. It has always been just around the corner as major battery companies make incremental gains on each of the three fronts. We’re still peering around that corner, but it feels like we’re really going to get there this time.
This corner is a big one, on par with the leap from nickel-metal-hydride batteries to lithium-ion a decade and a half ago. Rather than the incremental improvements we’ve seen so far this century, this promises to be one that kicks electric vehicles into an even high gear and wider adoption as range limitations shrink and safety concerns fade.
OEM Investment
If it were merely a matter of money, we would have found that corner some time ago. But even the substantial investments of the past are being dwarfed as automakers team with battery companies to ramp up production for the expected explosion of EV popularity. The investments are spurred by a variety of government mandates — some to decrease greenhouse gas emissions, others to subsidize electric vehicles and, most recently, the U.S. Inflation Reduction Act that will reward companies that use battery components from the U.S. or a trading partner.
That’s a problem right now, since Benchmark Minerals reports show 73% of the world’s cobalt and 59% of the lithium is processed in China. More than 90% of the world’s battery cathodes and anodes are produced in China. This is spurring an unprecedented wave of investment in American battery production as well as mining.
Toyota is planning to spend $2.5 billion on a cell-production plant in North Carolina. Honda is doing a $4.4 billion joint venture with LG Energy in Ohio. Panasonic, a longtime Tesla battery supplier, is looking into building a $4 billion battery plant in Oklahoma. Tesla itself has indicated it is looking into potentially setting up a lithium refining operation in Texas.
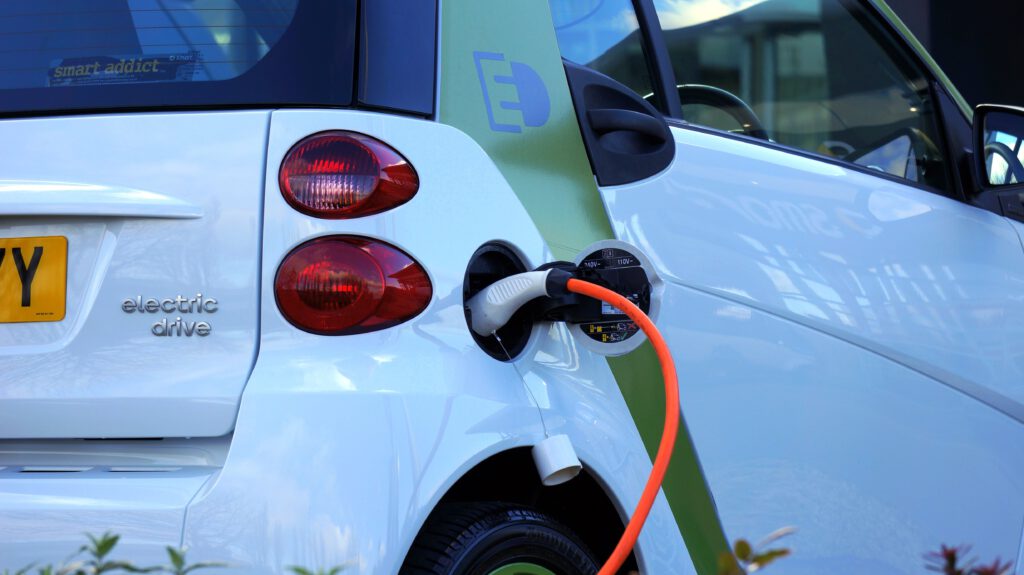
This follows massive multi-billion-dollar investments by General Motors, Ford and Stellantis to secure their battery supply chain in North America. Meanwhile, lithium mining is cranking up in the U.S. and the hunt is on for other minerals such as nickel. The brine of California’s Salton Sea is one source. The deserts of Nevada are another. Billions are flowing into those ventures and other mineral extraction plans to localize core American EV mineral resources.
The Hook-Ups
The push to localize the entire battery system is being done by a variety of start-ups and some established companies, almost all with substantial investment from auto companies and suppliers. The areas of innovation break down into two main areas — solid state batteries and materials beyond the standard lithium-ion chemistry.
Solid Power has already started small volume production of its solid state batteries, helping with support from Ford and BMW. QuantumScape is backed by Volkswagen and promises its batteries “soon.” Vietnamese newcomer to the U.S. market Vinfast is working with ProLogium from Taiwan and there’s speculation that the company’s next-generation models could contain solid state batteries. Vinfast has also said it will establish a battery plant near where it will locate its vehicle manufacturing operations. Li-Metal Corp. out of Canada is already functioning as a Tier 2 supplier, shipping samples of its solid-state style anodes to customers. It’s also working with Blue Solutions, a subsidiary of the French Bolloré Group and says it will have batteries in cars by 2026.
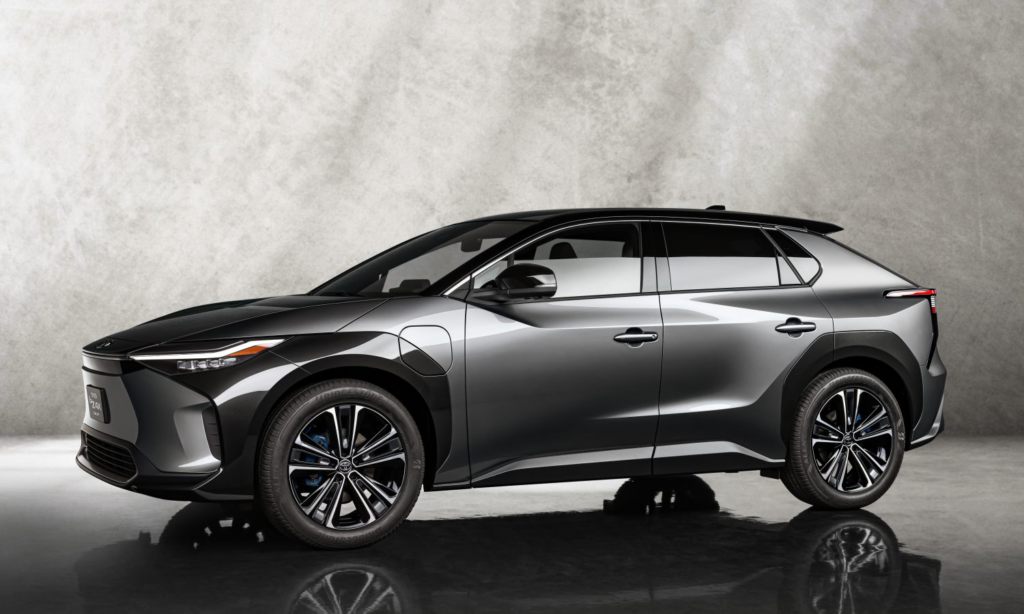
Then there are companies like Toyota, which has more solid-state battery patents than any of the large battery makers or other auto companies. A distant second in the tabulation by Nikkei and Patent Result was sometime Toyota battery partner Panasonic. Samsung from South Korea was the only non-Japanese company in the top 10, though the report noted that both LG Chem and Samsung have greatly increased their patent portfolios in the past three decades.
The State of Solid State
All this intellectual activity and money has moved the needle, as is evident by the close-in market predictions for the technology. The European environmental group Transport & Environment studied solid state batteries and found that — if the most sustainably sourced materials are used — this type of battery could reduce a car’s carbon footprint by as much as 39%. One caution was noted — solid state batteries actually require 35% more lithium than their predecessors, though they use far less cobalt and graphite. That could affect pricing and the promise of more battery power at less cost.
The solid state push and a concurrent move to reduce the environmental footprint of mining operations, have spurred new developments in the areas of mining and also recycling. Ionic Mineral Technologies recently emerged from stealth mode operations and is ramping up production of nano-silicon, which can be used as a replacement for graphite, promising increased energy density and faster charging speeds.
Tesla’s next-generation batteries have been delayed until 2023, according to Reuters, but when the production issues are overcome they are expected to bring about a $5,000 reduction in battery pack costs. That would be half the cost of the current generation battery packs.
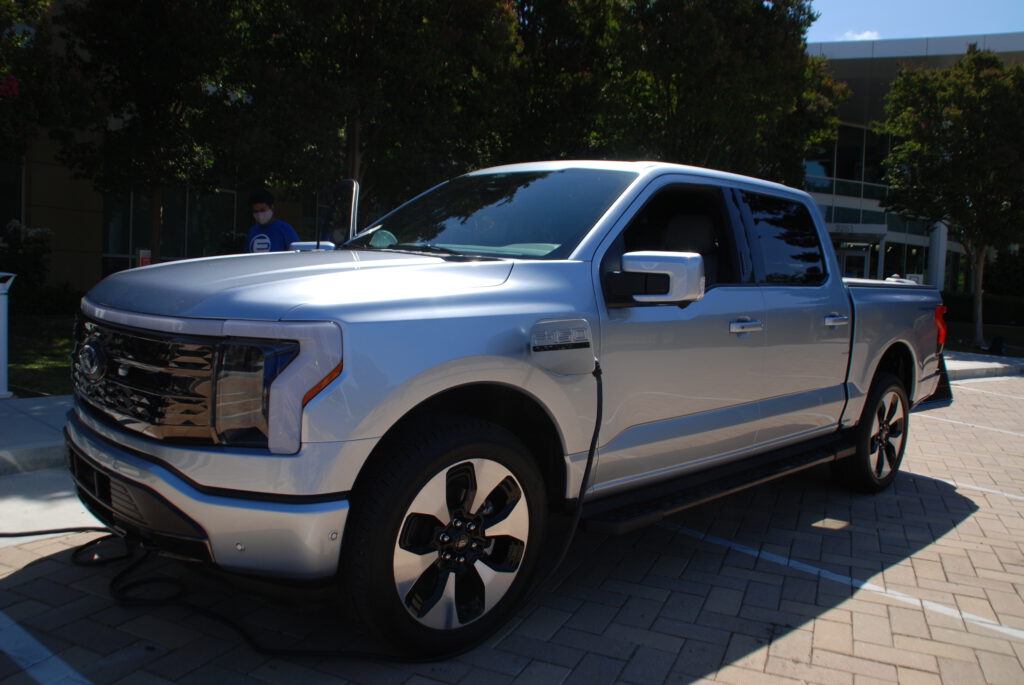
Another way to attack mineral scarcity and reduce cost is to use recycled components of the battery pack when it deteriorates and is no longer able to function as an automotive battery. Tesla’s J.B. Straubel quit the company he helped found to go into the battery recycling business. Another company to move into the space, Ascend Elements, has the support of Jaguar Land Rover and the South Korean conglomerate SK Group. Ly-Cycle Holdings is another new company moving into this space.
Alternatives to Solid State
New battery chemistries may give solid state batteries a run for its money. Addionics CEO Moshiel Biton, a battery expert, analyzed the various alternatives.
Lithium-iron-phosphate (LFP) batteries are safe and lightweight, but less energy dense than some other options. BYD and Tesla, two of the largest EV makers in the world, are fans.
Lithium-nickel-manganese-cobalt (NMC) batteries are more expensive than LFPs, but offer higher energy density. There are some concerns about high temperatures that could cause safety issues. LG is working on cobalt-free versions of the battery.
Using more silicon to substitute for graphite is one approach being tried. The concern with this approach, which Tesla is said to be exploring, is that while it is significantly cheaper than current chemistries, it may not be as stable or durable as other chemistries.
Sodium-ion batteries are a new approach that uses a cheaper material. Safer than LFP batteries, they have lower energy density. Giant Chinese battery maker CATL is working to improve this chemistry.
Then There’s Solid State
This one checks all the boxes — safer, more energy dense, capable of faster charging, greater range and longer life, but it’s current fatal flaw (other than not being in production) is cost. It’s still significantly more expensive to produce than the other chemistries, but given the amount of money being poured in this area, progress should be made relatively quickly. That corner we talked about earlier should be before the end of the decade.
It’s urgent because right now material costs — lead by lithium, cobalt and a variety of other critical materials — are skyrocketing and driving EV pricing up rather than down as production scales up. That corner, whether it’s ushering in solid state batteries or just a more advanced battery chemistry, cannot come too soon.